Max Release Paste Wax #2
Carnauba Based
12-ounce Net Content
and
Max Release Parting Film #10
PVA Based Parting Film
32-ounce Net Content
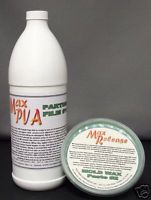
Or visit our eBay Store, PolymerProducts.
Description
The Best Mold Release Technique
Although we have tested and used this mold release technique in casting small flat pieces, finely detail replication to extra large applications (full scale automobile modeling), the user should always verify its effectiveness prior to use.
The combination of applying a paste wax on the mold first such as our MAX MOLD WAX #2 and then the MAX PVA PF#10 will serve many purposes that will save time and money. This release application technique will provide easy release, extend mold life and reduce or eliminate and cross contamination of the wax to the molded part. The molded part will often times require further finishing such as decorative painting or applying a protective coating. Any contamination that may have transfer to the molded part must be cleaned off, costing time, money and may pose adhesion problems of any subsequent coating application.
Apply as uniformly using a soft cloth. Buff away any build up especially on corners and sharp angles where it usually collects and then applying MAX PVA PF#10. This technique insures easy release from the mold while protecting the molded part from wax contamination.
Apply MAX #2 according to instructions prior to use of parting film.
MAX PVA PF#10 is ready to use as received and should not be diluted. It is best applied to mold surface using a spray gun although it can be brushed on depending on desired post-production finish.
Best results are achieved with as fine a spray as possible. To achieve this result, use a small orifice in the gun, close the needle about halfway, and adjust the air pressure to 80 – 100 psi at the gun (setting may vary depending on equipment used). Normal spraying distance is from 12 – 18 inches – MAX RELEASE PARTALL #10 should atomize prior to contact with mold surface.
Apply a thin mist coat first and allow to dry completely (approximately 10 – 15 minutes). Follow with two heavier flow coats, allowing each coat to dry completely before proceeding (approximately 30 – 45 minutes). A spray density that just allows the liquid to flow together and form a continuous film is ideal.
Dry film thickness must be at least 2 – 4 mils on new or reconditioned molds and 1 – 2 mils on seasoned molds (2 mils is the approximate thickness of an industrial-type trash bag). One gallon will cover about 400 square feet.
Drying time per coat is approximately 15 – 45 minutes (depending on thickness) with normal application. External factors such as humidity, proximity to sunlight, and the use of fans or heaters can cause drying time to vary. Film must be completely dry before proceeding with molding. Applying additional coats before a previous coat has dried thoroughly can compromise the ability to adequately protect mold surface and prevent part from sticking. Film should be very smooth and glossy when dry – a dull film may result from insufficient spray and may contain pinholes.
De-Molding the Part
The best procedure for separating the part from the mold depends on the size and shape of the part. In most cases the part can be lifted from the mold after loosening around the edges. A jet of air between the part and the mold at the edge is sometimes useful. On large curved parts it may be necessary to first tap over the surface with a rubber mallet. A very strong blast of air will free very rigid parts that cannot be flexed.
MAX PVA PF#10 will stay with the part or the mold and can be easily removed with water or a strong blast of air.
Warm water will work much faster than cold water dissolving the PVA FILM.
Do not use solvents to remove MAX PVA PF#10 as they will not be able to dissolve film – use water only.