Clear Liquid Resin-High Performance
Epoxy Resin System
The most crystal clear and color stable epoxy system commercially available
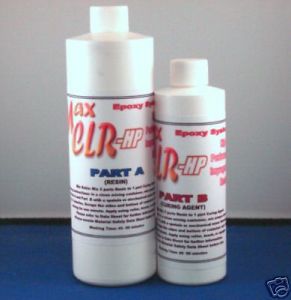
For ordering and inquiries please call 877-403-8008.
Or visit our eBay Store.
PolymerProducts on eBay
Available Kit Sizes:
Description
MAX CLR-HP A/B is a two-part epoxy based system specially formulated as High Performance version of the MAX CLR resin system. It offers higher mechanical performance while maintaining crystal clarity, gloss and other aesthetic qualities. MAX CLR-HP provides excellent performance at wider service temperature range, especially its retention of its mechanical hardness at elevated temperatures as well its durability when exposed to below freezing temperatures. Its none blushing performance, high gloss finish, excellent transparent clarity, color stability and ease of use make MAX CLR-HP an excellent choice as an impregnating resin for composite fabrics, protective coatings, casting resin and general fabricating applications.
MAX CLR-HP also offers high chemical resistance, structural adhesion and overall durability suitable for many protective coatings applications.
MAX CLR-HP A/B performs well at room temperature use and can withstand cyclic exposure to temperatures form -40°C to 112°C with minimal loss of mechanical performance.
MAX CLR-HP A/B can be as as an adhesive for bonding at variety of substrates such as composite materials, concrete and ceramic products, plastics, wood, glass, steel, aluminum and most soft metals.
Upon Cure, MAX CLR-HP A/B resists extreme and repeated thermal shocks making it well suited for bonding substrates with dissimilar expansion coefficients.
MAX CLR-HP A/B is 100% solids and does not contain Ozone Depleting Chemicals (ODC), non-reactive plasticizers or solvent fillers.
Physical and Mechanical Properties
Density |
1.10 G/CC |
Form and Color |
Clear Liquid |
Viscosity |
2,800 – 3,200 cPs @ 25ºC Mixed |
Mix Ratio |
50 Parts “B” to 100 Parts “A” By Weight |
Working Time |
45 – 50 Minutes @ 25ºC (100 Gram Mass) |
Peak Exotherm |
70ºC (100 Gram Mass) |
Thin Film Set Time |
4 to 6 Hours |
Handle Time |
8 Hours |
Cure Time |
2 to 7 days @ 25ºC or 8 hours at room temperature plus 1 hours at 100ºC |
Hardness |
80 ± 5 Shore D, |
Tee-Peel Strength |
5.7 Lbs. per inch Width |
Tensile Shear Strength |
2,935 psi @ 25ºC |
1,970 psi @ -40ºC |
|
1250 psi @ 100ºC |
|
Elongation |
3.0% @ 25ºC |
Flexural Strength |
13,000 psi |
Flexural Modulus |
344,000 psi |
Heat Deflection Temp. |
110ºC |
CHEMICAL RESISTANCE PERFORMANCE
FULL IMMERSION at 30°C
MEASURED PERCENT CHANGE IN WEIGHT
REAGENT |
3 days |
28 days |
Deionized Water |
0.49 |
1.50 |
Sea Water |
0.11 |
0.98 |
Methanol |
7.93 |
-2.41 |
Ethanol |
3.98 |
10.28 |
Toluene |
0.40 |
2.86 |
Xylene |
0.04 |
0.05 |
Butyl Cellosolve |
16.63 |
5.31 |
MEK |
Destroyed |
Destroyed |
10% Lactic Acid |
1.81 |
5.42 |
10% Acetic Acid |
0.11 |
0.45 |
70% Sulfuric Acid |
0.08 |
0.14 |
50% Sodium Hydroxide |
0 |
0 |
10% Sodium Hypochlorite |
0.51 |
1.36 |
SPECIMEN CURE CYCLE 7 days @ 25ºC plus 1 hours at 100ºC
1 CUBIC INCH SPECIMEN SIZE